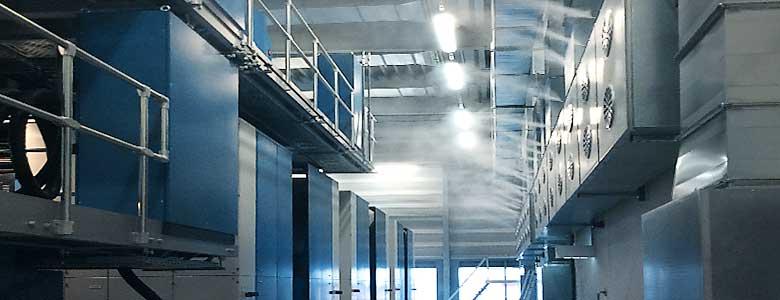
How humidity affects printing, or Hidden cause of huge losses.
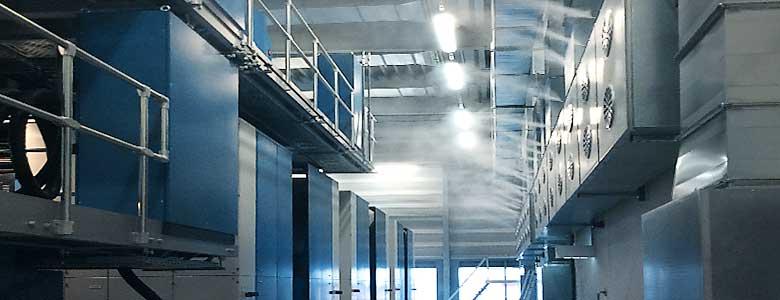
Hidden Printing Costs – Cost of Air
There are a lot of causes of print issues and, humidity is one of the most undervalued.
If we compare climate in Canada with the one in the continental Europe, Canadian environment is not very friendly for printing production. Very often, low humidity and hard water are the critical challenges for the print shops around the country. For example, in Calgary, it’s barely possible to run offset presses without air humidification and water softener. At the same time, Southern Ontario has much friendly weather conditions then beautiful Alberta. In Greater Toronto Area (GTA), water is relatively soft (8-12 dh) and, sometimes, we don’t need the water softeners to mix fountain solution. However, variable humidity of the air, especially in the winter time is very challenging.
Warm air can hold far more moisture than cold air, meaning that the relative humidity of cold air would be significantly higher than warm air if their absolute humidity levels were equal. When a furnace heats outside air in January from -15C to +20C, the internal air will carry only around 15% of water that cause a lot of issues in CTP room, Pressroom and Bindery.
In Offset Printing, dry air is the source of paper curl, size distortion, web breaks, paper cracking and static build up. Digital Printing and Flexo printing on self-adhesive materials are even more vulnerable. The issues that will occur if the relative humidity is lower than optimum level: Paper distortion. If relative humidity of the paper or carton board is low, the materials absorb the moisture from the air and from printing procedures. This leads to unwanted and often critical changes in the dimensions of the paper. The paper then is no longer flat and change dimensions going through the press. Doubling, register differences, creasing and distortion are problems very frequently encountered because of low humidity. Cracking. When relative humidity of the paper or carton board is low, the material will start cracking during die cutting and folding operations. Electrostatics issues. When paper is too dry during printing, we will challenge by electrostatic charges. The paper will stick together, misfeed. Also, creasing may occur.
In the winter timer, when external temperature is lower than -10C, the internal relative humidity falls till 15%. If the humidification system is down, functions improperly or not enough for the area, it will bring a lot of challenges for all company. From my personal experience, with humidity under 20%, the average idle time of the offset press due to paper distortion and misfeed is 60 min. per one press per shift.
The average cost of press time for 6-8 colour 40′ Offeset Printing Press is CAD 600 per hour. So, direct losses may be CAD 600 per one press, only per one shift. If we multiply CAD 600 to the shifts and press numbers, the amount will be tremendous. For example, if there are 3 presses working 3 shifts, the direct losses for the company will be around CAD 6.000 only per one day.
Definitely, high qualification of press crews and instant troubleshooting may minimize this catastrophe, but the consequences of this accident will chased the company during next few weeks on bindery and die cutting department.
The proper level of humidification is very important for the print shop. The optimum relative humidity for sheet-fed, digital printing, paper storage and bindery should be 50±5%. Optimum level of relative air humidity significantly helps to standardize the printing process, drastically reduce spoilage and prevent equipment idle time.
Copyright © Dmytro Tuzov, ca.linkedin.com/in/dtuzov/, February 2017